
A Wool by Any Other Name
Contrary to popular belief, Rockwool is actually not the proper, formal term for the insulating material that is mineral wool. Mineral wool, also known scientifically as Man-Made Mineral Fibres (MMMF), is a broad term for a fibrous inorganic substance made primarily from rock, clay, slag, or glass. But what exactly is mineral wool, and what are the key differences between these types?
Origins of Mineral Wool
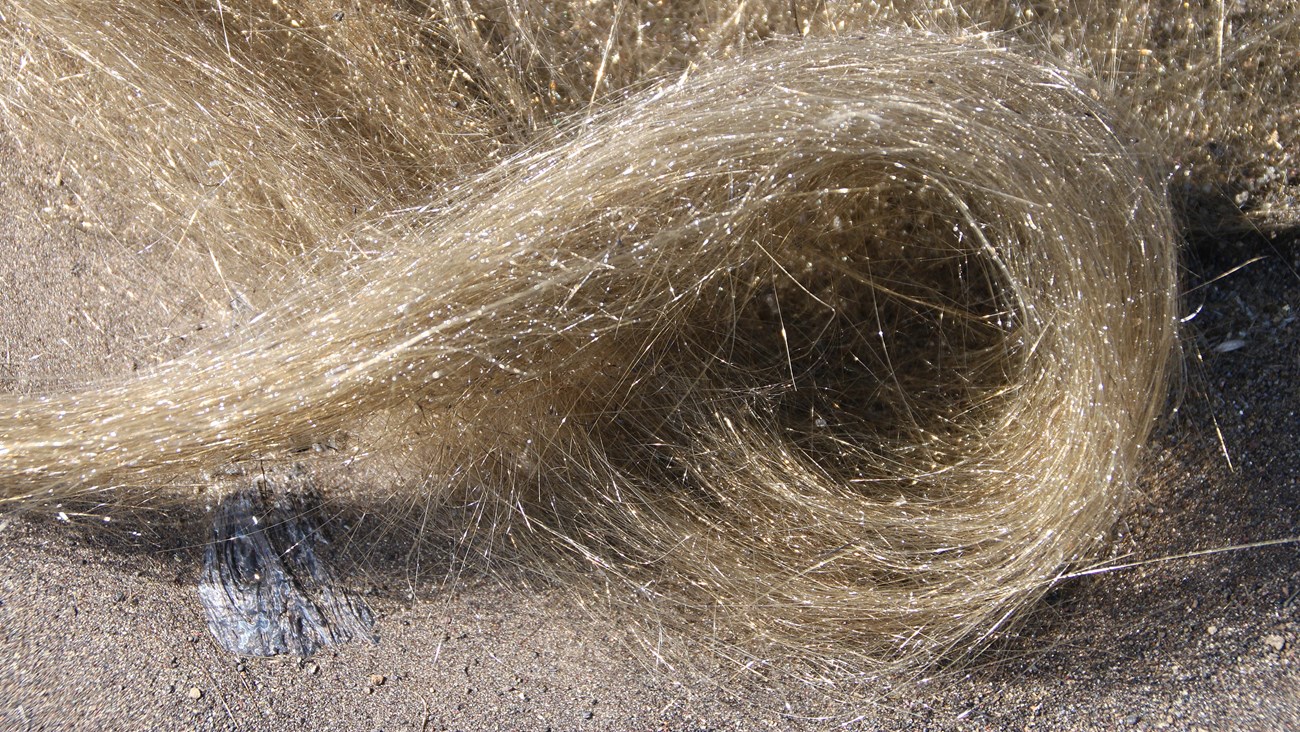
Mineral wool was first discovered in Hawaii in the early 1900s in its natural form. When the active shield volcano Kilauea erupted, thin, fine strands of volcanic slag formed as a by-product. These volcanic glass patterns, fondly called “Pele’s hair” after the Hawaiian goddess of volcanoes, form naturally during eruptions when high winds blow across lava streams of basalt, creating thin fibrous strands. These delicate strands are often found and commonly gather on high places such as treetops and electric poles, but due to its very brittle and sharp nature, it is not advised to touch and handle the material with bare hands as small, broken pieces can easily enter the skin.
Apart from Hawaii, Pele’s hair or mineral wool in its natural form has been produced by volcanoes across the globe in Nicaragua, Italy, Ethiopia, and even Iceland, where it is known as nornahár or “witches’ hair.”
How Mineral Wool is Made
It was only in 1953 when mineral wool intended for high-temperature applications was commercially viable, after it was invented in the United States in 1942. Because the material is made to withstand and resist temperatures above 1,000°C, there are several key steps it must undergo to be effective:
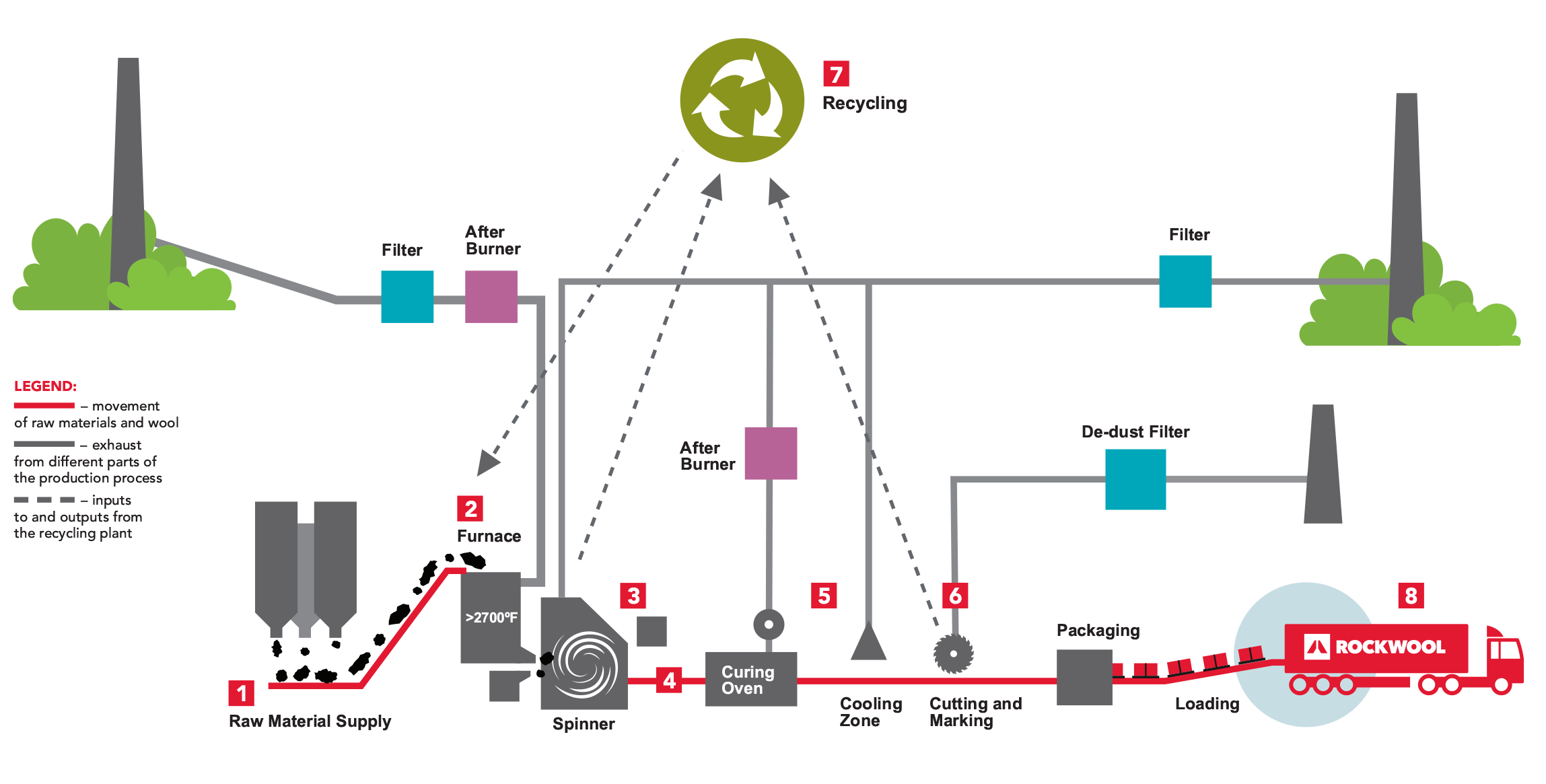
- Melting: Pre-heated raw materials are mixed with coal, natural gas, and combustion air in a furnace, reaching temperatures above 2700°F to create a molten mixture.
- Spinning: The molten material then flows from the furnace onto spinning wheels, where powerful air streams draw the fibers into fine strands—similar to the natural occurrence of Pele’s hair. During this process, binder and cooling water are added to the fibers, while de-dusting oil is applied to enhance water repellency and reduce dust formation during cutting and in the finished products.
- Collection: The fibers are collected on a large rotating drum and dropped onto a conveyor in thin layers, which are then uniformly layered to achieve the desired thickness.
- Curing: Lastly, the layered wool is conveyed into a curing oven, where water is evaporated, and the binder is cured with hot air. Afterward, the wool is cooled using ambient air to ensure stability and durability.
-
Stone, Glass, Ceramic, or Slag? What’s the Difference?
While the process of creating mineral wool essentially remains the same, several materials can be added and combined to produce different types of mineral wool, each with their own unique properties.
- Glass Wool: Made from spun silica, it is lightweight and offers decent insulation, though its fibers are not as compact as other types.
- Ceramic Wool: Made from spun clay, it boasts excellent resistance to chemical corrosion and high temperatures, making it ideal for industrial applications. However, its insulation properties are moderate, and its fibers are less compact.
- Stone Wool: Produced from spun volcanic rock like basalt, it has superior insulating properties. Its fibers are more intact and compact, making it ideal for interior insulation applications.
- Slag Wool: Made from byproducts of iron refining such as blast furnace slag, it contains many impurities, which can affect its overall performance compared to other mineral wools.

Picking the Right One for Your Home
For the untrained eye, distinguishing between different types of mineral wool insulation can be difficult. The best way to ensure that you are getting the right insulation material is by studying and assessing each type against your building needs, checking certifications and documents such as Technical Data Sheets and Material Testing Data Sheets to verify quality and performance, and purchasing from reputable brands like Rockwool and credible distributors and suppliers.
At KITCI, we are committed to helping you identify and procure the right materials, ensuring that your building and insulation needs are met with high-quality, certified materials and with service and expertise you can trust.
